Na desetiny milimetru: Jak při výrobě aut pomáhá fotogrammetrie 14.6.2022
V moderním automobilovém průmyslu je vysoká přesnost výroby nutností. Preciznost výroby má totiž vliv na důležité aspekty automobilů, jako jsou provozní vlastnosti nebo bezpečnost. K co nejpřesnější výrobě patří nejen patřičná výrobní technika, ale také zařízení a způsoby, díky kterým je možné přesnost výroby kontrolovat. K nim patří mimo jiné fotogrammetrie, jež se využívá pro měření tolerancí karoserií a lze díky ní rychle rozeznat odchylky s přesností na desetiny milimetru.
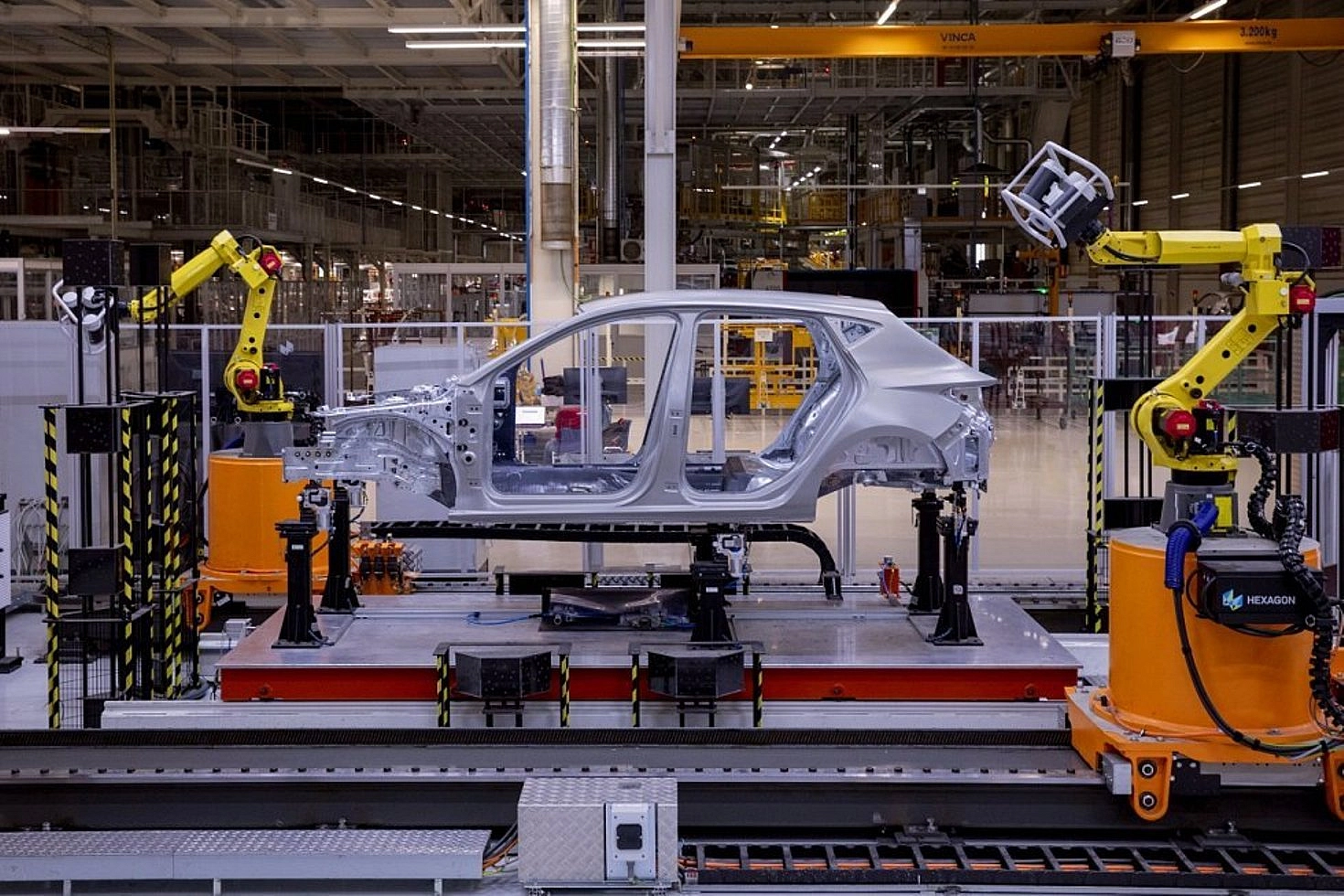
SEAT průkopníkem
První automobilkou, která v sériově výrobě začala využívat fotogrammetrii pro průběžné automatizované měření ve velkém měřítku, byl SEAT při výrobě modelů SEAT Leon a CUPRA Formentor. Tuto bezkontaktní technologii měření má v automobilce na starosti oddělení technologie měření a modulárního fixačního systému. Ještě donedávna měření karoserií probíhalo částečně manuálně, ale díky zavedení fotogrammetrie již není manuální měření potřeba. Přesná a rychlá technologie měření výrazně zvyšuje efektivitu v rámci celého měřicího procesu při výrobě vozů na montážní lince.
Co je fotogrammetrie
Fotogrammetrie je obor zabývající se měřením rozměrů z fotografických snímků. Ve světě automobilů se konkrétně tato technologie bezkontaktního optického měření používá tak, že se pořídí fotografie prověřovaného dílu karoserie a dojde na něm k zaznamenání pozice milionů bodů. Díky přesnému změření pozice takového počtu bodů na měřeném dílu se následně v příslušném programu vytvoří barevná mapa zobrazující případné odchylky od požadovaného tvaru a rozměru. Na výsledném snímku kontrolní pracovníci zřetelně vidí 100 % geometrických linií jak v exteriéru, tak interiéru automobilu a mohou tak snadno zkontrolovat, zda je kontrolovaná oblast v pořádku.
Jak probíhá měření ve výrobě
Kontrola se vzhledem k objemu produkce tak velké automobilky, jako je SEAT, provádí u náhodně vybraných součástí z montážní linky během každé výrobní směny. Náhodně vybrané díly se podrobují velmi důsledné kontrole poté, co je automatizovaní roboti přepraví do měřicí haly s rozlohou 1500 metrů čtverečních. V této hale měření zajišťují speciální měřicí zařízení vybavená kamerami.
Nepřetržitý náhodný výběr komponentů k měření zaručuje to, že všechny vozy odjíždějící z montážní linky výrobního závodu mají takové rozměry, jaké mít mají. Po celou dobu výroby modelu. S přesností na desetinu milimetru. V případě, že by se u některého dílu objevil problém s nedostatečnou přesností výroby, okamžitě se může začít hledat příčina problému a jeho řešení. Samozřejmě se také zajistí další díly, u kterých bude riziko stejné nepřesnosti. Nehrozí tedy, že by se do vozů dostaly součásti nevyhovující stanoveným standardům.
Čím více bodů, tím vyšší přesnost
Pro vysokou přesnost měření je zásadní velký počet bodových měření na celém dílu. Měření přitom probíhá u všech dílů, ze kterých se karoserie automobilu skládá. „Stroje pořizují celkem 200 až 300 snímků u montážních celků a 1000 fotografií u skeletu karoserie, což je ekvivalentem sedmi milionů bodových měření u montážního celku a až 98 milionů u celého skeletu,“ říká Pedro Vallejo, vedoucí oddělení technologie měření a modulárního fixačního systému ve společnosti SEAT. Kontrolní pracovníci každý den analyzují data získaná z 9000 snímků, respektive až 210 milionů bodových měření.
Zkrácení času měření
Optické měření přispívá k vysoké efektivitě výroby svou přesností a rovněž rychlostí měření – ve srovnání s konvenčními metodami dotykového měření dosahuje úspora času až 90 %. „Dříve jsme změřili tři díly za den, zatímco nyní jich kontrolujeme 30 denně. To nám umožnilo zásadně změnit způsob, jímž jsme pracovali v uplynulých 20 až 30 letech. Zaměstnance jsme proškolili pro používání metod, které jsou náročnější na kvalifikaci, a exponenciálně vzrostlo množství získávaných informací, abychom mohli zákazníkům dodávat automobily v nejvyšší možné kvalitě,“ vysvětluje Pedro Vallejo.
Měření čeká další vývoj
Ačkoliv je optické bezkontaktní měření již v současnosti mimořádně efektivní a přínosné, do budoucna se počítá s jeho dalším významným vylepšením. Všechna získávaná data z měření se uchovávají a analyzuje je algoritmus strojového učení, který se zaměřuje na zjišťování četnosti jakýchkoliv odchylek. Dnes měření umožňuje najít až vzniklé chyby a teprve následně na ně reagovat, zatímco díky programu schopnému rozpoznat četnost opakování různých druhů odchylek bude možné nepřesnosti výroby předvídat a reagovat na ně s předstihem, aby k nim vůbec nedošlo. Program totiž bude na základě obrovského množství dat vytvářet předpovědi o potřebách změny nastavení výrobních strojů, které se na výrobě dané součásti podílí.